Activated carbon has been developed for the effective desulphurisation (H2S removal) of siloxane removal and VOCs from agricultural biogas, wastewater treatment plants and landfill gas, which is particularly important for environmental protection and increasing energy efficiency. The removal of contaminants from biogas not only protects the installations from corrosion, but also improves the quality of the fuel, allowing it to be used safely for the production of electricity and heat.
Activated carbon
Products:
Activated carbon for hydrogen sulphide removal: Activated carbon for siloxane removal:Ammonium nitrogen fixing preparations
The problem of excessive amounts of ammoniacal nitrogen in the digestion mass is an increasingly frequent problem in Polish biogas plants. This is due to the fact that more and more by-products and waste from the agri-food industry are being used, in particular materials of animal origin that are rich in nitrogen, such as chicken manure, flotation sludge or dairy waste. Nitrogen is essential in the methane fermentation process (C:N ratio) for the proper conversion of organic compounds into biogas. However, at higher concentrations (> 3500 mg/l), it starts to have an inhibitory effect on the methane fermentation process. Ammonium inhibition is indirectly due to the fact that ammonium ions (NH4+ ) contribute to an increase in the pH of the digestion mass above > 8.00, which is no longer the optimum environment for methane bacteria. In addition, in alkaline environments and at elevated temperatures, ammonium ions convert to ammonia (NH3 ), a compound that is toxic to biogas-producing bacteria.
In response to market demand, we offer an effective preparation of MiaMethan® A-min to fix excessive amounts of ammonium nitrogen from the digestion mass. Our product can be used continuously or intermittently.
Products:
Biogas analysers
Biogas analysers are one of the most important measurement components in a biogas plant.
These instruments allow for periodic or continuous measurement of the biogas composition to optimise plant operation by being able to monitor the biogas composition and control the process in the digesters. Using the analyser, we are able to assess the level of methane, hydrogen sulphide, oxygen, hydrogen, ammonia carbon monoxide or carbon dioxide. This type of equipment is used to analyse the composition of biogas produced in agricultural biogas plants, industrial biogas plants, wastewater treatment plants and landfill sites.
As the demand for reliable, precise, and economical biogas measurement systems has increased in recent years, you will find in our product range both stationary and portable gas analysers from the BINDER GROUP, which have been successfully used in installations all over the world for many years.
Products:
Mobile biogas analysers: Stationary biogas analyzers – basic version: Stationary biogas analyzers – premium version: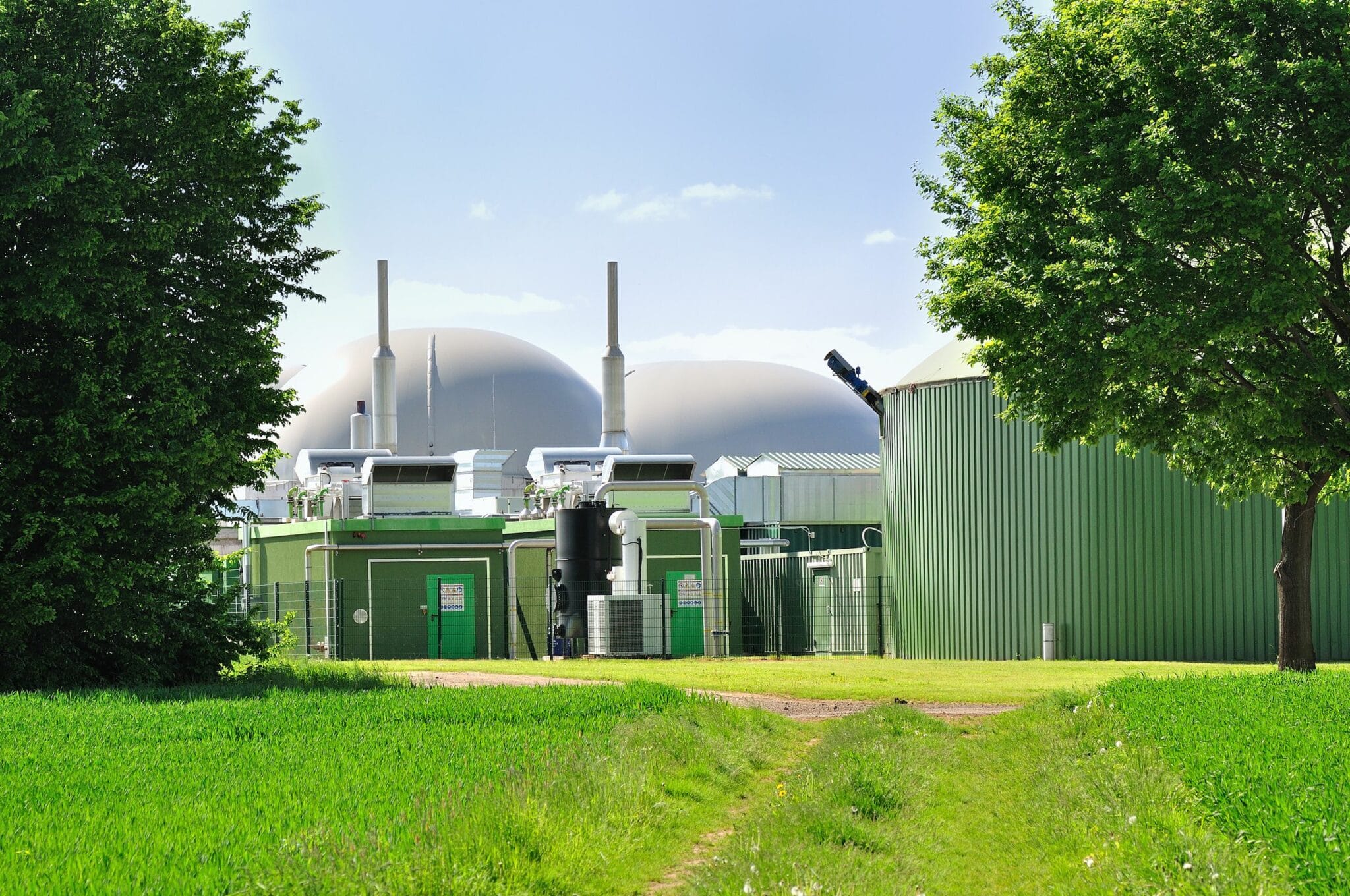
Desulphurisation of biogas
Efficient biogas desulphurisation is one of the key biogas treatment processes determining the stability of energy production in biogas plants. This is due to the fact that hydrogen sulphide, even in small quantities, has a damaging effect on technical plant components with which it comes into contact, such as unprotected fermentation tank walls, gas pipelines or valves. Excessively high concentrations of hydrogen sulphide in biogas (gas engine manufacturers allow maximum levels of H2 S of up to 150-200 ppm), contributes to a shortened service life of CHP module components (e.g., spark plugs) and the need for more frequent replacement of consumables (engine oil, filters). This in turn contributes to more frequent downtime of the CHP unit, resulting in increased operating costs. Disregarding the importance of the desulphurisation process, particularly operating on highly sulphurised biogas, practically always results in serious failures of the cogeneration units, the costs of which are often calculated in hundreds of thousands of zlotys.
Our product range includes field-proven products and systems for biogas desulphurisation, which have been successfully used for many years in installations such as agricultural biogas plants, industrial/utilisation biogas plants and biogas plants at sewage treatment plants.
Our product range includes field-proven products and systems for biogas desulphurisation, which have been successfully used for many years in installations such as agricultural biogas plants, industrial/utilisation biogas plants and biogas plants at sewage treatment plants.
Products:
Enzyme preparations
Enzymes in fermentation accelerate the decomposition of complex organic compounds. The main source of such compounds are substrates of plant origin, e.g., cellulose, and xylose. Without the right enzymes, these substrates are broken down only slightly, causing the digestion mass to thicken and increase viscosity, which in turn can translate into mixing and pumping problems and the appearance of dross that hinders fermenter degassing. The addition of adequate enzymes accelerates the breakdown of complex organic compounds into simple compounds, which are more easily broken down by bacteria and enzymes produced by them. This results in better substrate attenuation and lower density of the digestion mass, which translates into reduced costs and higher biogas production.
Products:
FOS/TAC measurement kit
What are FOS, TAC and the FOS/TAC ratio?
FOS – the abbreviation comes from German and stands for Flüchtigen Organischen Säuren, that is volatile organic acids (C2-C6). These are compounds formed during phases II and III of the methane fermentation process. In English-language literature the abbreviation FOS is VFA or volatile fatty acids. The FOS value is determined by titration and represents the sum of all volatile acids converted to acetic acid. The most commonly used unit for its determination is mg/l or g/l.
TAC – this abbreviation also comes from German and stands for Total Alkalischen Carbonaten. TAC defines the total inorganic carbonate buffer solution. The TAC is also determined by titration and represents the sum of all buffering substances (i.e., substances that protect against a drop in pH), including carbonates, ammonium ions and phosphates. The TAC is expressed as carbonate (CaCO3 ), the unit used being mg/l or g/l.
FOS/TAC – is a parameter characterising the equilibrium state between volatile organic acids (FOS) and buffering agents (TAC). It is represented as a fraction, with TAC [mg/l] in the denominator and FOS [mg/l] in the numerator.
Products:
Gas flow meters
Thermal flowmeters are designed to measure the flow of gases.
Flow meters of the COMBIMASS® eco bio+ series have been developed specifically for the measurement of digester gas flow and cover a wide range of applications in biogas plants. The instruments can be used for process temperatures of up to 130°C.
The device was developed using thermal dispersion technology. This principle directly determines the gas flow under normal pressure and temperature conditions.
The technology used is excellent for wet biogas applications, as even at low gas velocities the measurement is highly accurate.
The use of this type of device will help to increase control over typical problems occurring in installations and also reduce the likelihood of failure.
Products:
Micronutrients for biogas plants
Micronutrients are metal ions that are present in the digestion mass and are supplied on an ongoing basis with the substrates. In order to maintain adequate biogas production capacity and proper decomposition of organic compounds, it is important to have an adequate concentration of the following elements in particular: nickel (Ni), cobalt (Co), selenium (Se), molybdenum (Mo), manganese (Mn), zinc (Zn), iron (Fe), copper (Cu), vanadium (V), potassium (K), calcium (Ca), magnesium (Mg), and sulphur (S).
Metal ions are essential elements for the catalytic activity of the enzymes produced by bacteria, which are responsible for transforming the compounds that ultimately produce biogas. For example, nickel is a major component of the coenzymes F420 and F430, which are important hydrogen carriers in the formation of methane.
In the event of a deficiency of any of these micronutrients, methane fermentation is destabilised. The main symptoms are a reduction in yield and a deterioration in the quality of the biogas produced. There is also a deterioration in the biotechnological parameters of the process, such as an increase in the level of volatile fatty acids and a change in the profile of VFA.
The solution in this case is to use a suitable micronutrient preparation from our offer. Depending on your needs, these may be single or multi-constituent preparations that will quickly restore the balance of biochemical processes.
Such products can be used continuously or on an ad hoc basis. Often, their use improves gas yield by a few to over a dozen per cent from the same input, depending on the individual situation. In addition, it stabilises the process so that the bacteria, given optimum growth conditions, are able to adapt to fluctuating feedstock streams and higher organic loadings.
In the case of dedicated preparations, the selection of micronutrient doses should be preceded by a laboratory test determining the current concentrations of the individual elements. On this basis, both the composition and doses of preparations for specific installations are selected. Regular check-ups make it possible to optimise the supply of a dedicated preparation.
Products:
Individually prepared micronutrient mixtures to meet customer needs: First aid for acidification / overfeeding of biogas plants: Standard preparations in liquid form:Silage additives
Silage additives are preparations that accelerate the ensiling process by increasing the multiplication rate of lactic acid bacteria. The accumulated lactic acid acidifies the environment and limits the growth of yeasts and moulds, thus protecting the silage from deterioration of quality parameters.
The aim of using ensiling additives is to rapidly reduce the oxygen content of the material and to increase the acidity, which influences the faster growth of lactic acid bacteria to stabilise and preserve the ensiled material. Silage additives are divided into two groups: stimulants in the form of bacterial inoculants and inhibitors. Inoculants contain inactive bacteria that are activated in wet material. They promote the growth of lactic acid bacteria and the production of acids, resulting in a faster drop in pH. Inhibitors help to slow down unwanted silage degradation caused by yeast and mould growth or to reduce the breakdown of plant proteins.
The silage additives in our offer include many additives with alternative functions.
Products:
Skimmers for biogas plants
Foam in anaerobic digestion plants is a common operational problem that needs to be tackled systematically. In the absence of preventive action on the part of biogas plant personnel, there can be periodic production stoppages in the biogas plant resulting from the foam entering safety valves, gas pipelines, drainage, clogging biogas dryer exchangers or gas compressors. In extreme cases, membrane roofs can be damaged, causing a costly shutdown of a biogas plant for weeks. The most common causes of foaming include the use of protein-rich substrates, raw materials with pH distinctly different from that of the digestate, and the use in a short time large quantities of substrates rich in easily decomposable compounds (e.g., simple sugars).
Common substrates often ‘responsible’ for foam formation include potatoes, potato pulp, sugar beet pulp and protein-rich animal products such as dairy waste.
Products:
system bioGASMAS
As the only distributor of bioGASMAS on the Polish market, we offer a state-of-the-art biogas and biomethane plant management tool that allows owners and operators of these plants to have full control over the production process. Our system provides detailed information in real time, enabling quick decisions and optimisation of raw material consumption.